Your workforce is your greatest asset—but haphazard labor budgeting can weigh your organization down rather than boost profits.
Direct labor costs include the wages and benefits of employees directly involved in producing goods or delivering services. Although the cost of direct labor is straightforward to calculate, it still requires careful tracking and analysis to account for every dollar.
In this article, we’ll demystify direct labor, distinguish it from indirect labor, and learn how to calculate direct labor costs effectively. With a few helpful equations, you’ll be able to take advantage of your business’s greatest strength.
What is direct labor?
Direct labor refers to work performed by employees who are directly involved in producing goods or providing services. Its costs include the salaries and wages paid to workers whose efforts are directly linked to specific products or projects.
Direct labor examples include a machine operator who works on an assembly line and an accountant who provides services to several clients. These workers’ efforts are directly tied to the creation of the end product or service.
Direct vs. indirect labor
Unlike direct labor, indirect labor involves employees who support the production process but aren’t directly involved in creating goods or services. Examples of indirect labor include maintenance staff, supervisors, and administrative personnel.
Although indirect labor is essential for overall operations, its costs are categorized as overhead rather than directly linked to production value.
Estimating direct labor cost
Many businesses use a standard hourly rate to roughly calculate labor costs and quickly estimate budgets.
For example, imagine an assembly worker who manufactures computer processors. Their hourly wage is $25 per hour, and each computer processor takes 15 minutes to assemble. The estimated direct labor cost to produce 500 computer processors would look like this:
$25 x 0.25 hours x 500 units = $3,125
This direct labor cost formula helps companies process payroll, project operational budgets, and calculate the cost of new employees.
However, the true cost of direct labor goes beyond gross pay and hours worked. Companies should examine every expense tied to hiring and retaining employees to clearly visualize direct labor costs.
Direct labor’s total cost includes regular payroll taxes, including Social Security taxes, Medicare taxes, unemployment taxes, and workers’ compensation insurance. There are also variable costs, including employee benefits like health insurance, pension plan contributions, overtime hours, and training and development expenses.
How to calculate direct labor cost
Accurate labor cost estimations are crucial to evaluate your workforce’s efficiency compared to industry standards. A comprehensive cost formula will capture the total expense of your workforce so you can avoid underestimating overhead costs that could negatively impact profitability.
Here’s a step-by-step guide to calculating direct labor costs:
1. Calculate direct labor wages
Start by determining the direct labor hourly rate, including base pay, benefits, and payroll taxes. To find the wage rate, add the total value of benefits and payroll taxes and divide by the total number of hours worked in the relevant pay period.
For example, suppose employees earn $30 per hour, and you pay out $300 in benefits and $150 in taxes for every 40 hours of work. First, add the benefits and taxes to get $450. Then, divide by 40 to arrive at $11.25. Add this to the base pay, and you’ll find an hourly rate of $41.25.
2. Determine direct labor hours per unit
Next, calculate how many direct labor hours are required to produce one unit. Divide the total number of hours worked by the number of units produced. For example, if 50 hours are needed to produce 500 units, then each unit requires 0.1 hours of direct labor.
3. Calculate labor cost per unit
To find the direct labor cost per unit, multiply the direct labor hourly rate by the time required to produce one unit. Using the previous example, if the hourly rate is $41.25 and it takes 0.1 hours to make a single unit, the cost per unit is $4.13.
4. Determine the variance between standard and actual labor costs
Standard costs are the expected cost of materials, labor, and overhead based on industry benchmarks and operating conditions. To find the variance, subtract the standard cost from the actual labor cost. If the actual cost is higher than the standard, your operational output has inefficiencies or unnecessary expenses. If the actual cost is lower than the standard, you have above-average operational efficiencies.
How to lower direct labor cost
Successful businesses constantly evaluate how much employees cost and seek to strengthen operational efficiency. Reduced labor costs improve your bottom line and free up resources for other strategic initiatives, like improved benefits packages or better tools.
Here are four approaches for more effective cost management:
1. Reduce absenteeism
Chronic absenteeism impacts an organization’s bottom line with costs that aren’t always easy to track. When employees frequently miss work, management may scramble to find temporary replacements or pay overtime to replacement staff. This extra expense and inefficient resource allocation can quickly strain a business’s finances. Additionally, frequent absences jeopardize production schedules, delay projects, and diminish team morale.
Absenteeism doesn’t have a one-size-fits-all solution. Analyze the underlying causes of poor attendance (e.g., general workplace dissatisfaction or personal issues). Once you identify the root cause, you can develop targeted strategies to address it, such as improving company culture, enhancing employee support programs, or offering flexible work schedules to employees and independent contractors.
2. Adjust business operating procedures
Inefficient operating procedures can silently chip away at your budget, leading to wasted time or unnecessary labor costs. Disorganized or outdated workflows may lead employees to spend more time on tasks or even duplicate each other’s efforts.
To tackle this issue, evaluate your current business processes to find inefficiencies and bottlenecks. Streamline procedures by adopting lean methodologies, investing in more efficient technology, or reorganizing workflows to eliminate redundancies. With some tinkering, you can ensure every dollar contributes to your business goals.
3. Track time
Inaccurate time tracking can significantly impact the cost of goods by creating payroll errors, unplanned overtime, or unproductive time. Typically, manual or outdated systems cause inefficiencies and inaccuracies that inflate direct costs.
A modern time-tracking system provides precise, real-time data on employee hours. It will help you manage labor costs, streamline payroll processes, and maintain more financial control over operations.
4. Cross-train employees
Underutilized employees and workers with limited skill sets generate labor costs while offering limited returns, especially during peak periods or staff shortages. You may need to hire independent contractors or pay overtime to cover gaps when employees are only trained for specific tasks.
Cross-train employees to perform multiple roles for greater flexibility in managing workforce resources. You will need to budget for upskilling and cross-training, but an agile team with diverse skills will strengthen productivity, improve morale, and optimize labor resources.
Manage and optimize labor costs with Oyster
Your workforce is your most vital resource. A well-managed global team should boost profitability, not drag down your bottom line. You should manage direct labor costs effectively to maximize operational efficiency and productivity. An experienced collaborator can help you navigate the complexities of HR and labor management so you can focus on keeping costs down, productivity up, and employees happy.
With Oyster’s global employment platform, you can effortlessly calculate global salaries and streamline payroll in over 180 countries worldwide. Discover how Oyster can help you manage and optimize your workforce with ease. Get started with Oyster today.
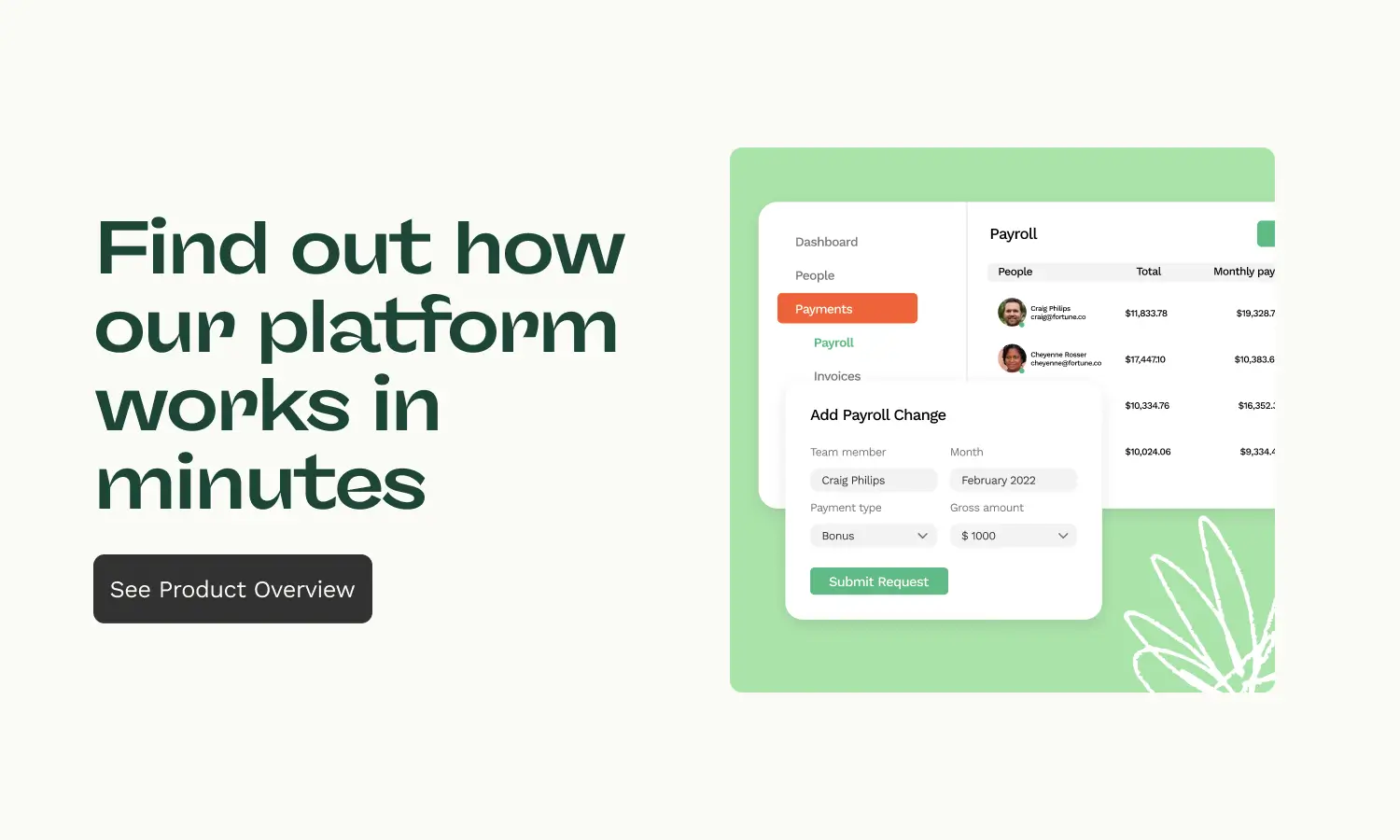
About Oyster
Oyster is a global employment platform designed to enable visionary HR leaders to find, engage, pay, manage, develop, and take care of a thriving distributed workforce. Oyster lets growing companies give valued international team members the experience they deserve, without the usual headaches and expense.
Oyster enables hiring anywhere in the world—with reliable, compliant payroll, and great local benefits and perks.